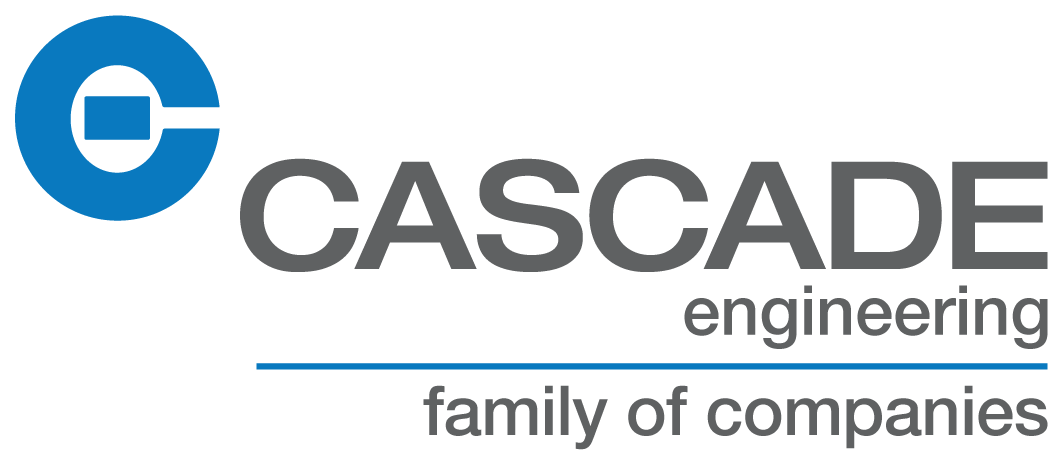
Innovation means knowing something works, but being determined to make it better. It’s looking past limits and common perceptions. It’s having the courage to act on unusual ideas—especially ones that make the world better. Whether it’s a new method, technology, or product, innovation is at the heart of everything we do.
The growth of electric and hybrid vehicles in the transportation market offers exciting experiences for consumers, but also demands innovative solutions for new technology applications. Cascade Engineering is collaborating with partners on a global scale to develop light weight, cost competitive solutions for battery components for a variety of electric vehicle markets. We offer solutions in part consolidation, fluid management, and weight reduction for products ranging from battery components to large structural enclosures.
Reducing the carbon footprint of our materials and processes is an important responsibility for building a sustainable future. In cooperation with UBQ Materials, Cascade Engineering is integrating household waste, diverted from landfills into usable material, into the products we manufacture. Eliminating waste from the landfill reduces the amount of methane gas in the environment, and when used within our products, results in a climate positive product. As the worldwide need for plastics continues to grow, the planets need for climate positive solutions grows as well.
Once China implemented the Green Fence and closed their borders to US recyclables Cascade Engineering partnered with Waste Management and The Recycling Partnership to design a solution to the problem of recycled plastics not having a home. We created pull in the US supply chain model by collecting mixed bulky rigid plastic from residential curbside recycling programs, sorted at the WM MRF, KW Plastics processed it and then Cascade Engineering reintroduced it into manufacturing and made new carts. Collectively we saved the recycled plastic from landfill and upcycled it into brand new product of high value.
When weight reduction is key, we lend our expertise in metal-to-plastic conversion. A strategic combination of material selection, part design, feature integration, and finishing enables a successful transition from metal to plastic, reducing a part’s weight and material.
Creating maximum acoustic performance with the lowest possible mass, we can reduce noise, vibration, and harshness with a combination of injection molding and specialty fibers. We can also integrate features such as molded-in hinges.
Fully recyclable and designed with Design for Environment (DFE) principles, the Decade's RACX® Pallet is fabricated of 100% recycled HDPE plastic and combines strength and economy in a lightweight, one-piece design. With an evenly distributed load, the pallet offers unsupported rack capacities up to 2,200 lbs.
Intelligence now comes encapsulated in plastic. Our RFID tags are shining examples of what happens when materials and technology are integrated as one. Today, this innovation can track resources in virtually any environment. Into the future, we expect to find new and innovative uses based on our ideas and the needs of the companies we work with.
Integrating plastic with technology can solve problems and make business a whole lot easier. Our most successful application to date is Cart Logic—a web service and mobile app designed for the waste and recycling industry. As we progress into the future, the implementation of technology is an area we plan on pursuing more and more.